Cette question représente un défi important mais également une opportunité pour rendre ce secteur plus durable. Les prothèses, orthèses et podo-orthèses modernes sont souvent fabriquées à partir de matériaux composites, tels que les fibres de verre, les fibres de carbone et/ou carbone et verre mêlées (parfois kevlar), associées à des résines polymères. Ces matériaux sont privilégiés pour leur légèreté, leur solidité et leur durabilité. Cependant, leur complexité rend le recyclage plus difficile que celui des matériaux plus traditionnels comme le métal ou le plastique.
Défis du recyclage des matériaux composites
- Composition hétérogène : Les matériaux composites sont constitués de plusieurs éléments (fibres et résines) fortement liés, ce qui rend leur séparation et leur récupération complexes.
- Résistance chimique et thermique : Les résines utilisées dans ces composites sont souvent thermodurcissables (même si certaines disposent de propriété thermoformable), ce qui signifie qu’une fois durcies, elles ne peuvent pas être refondues, contrairement aux résines purement thermoplastiques. Cela limite leur recyclabilité par des procédés traditionnels.
- Coût élevé des technologies de recyclage : Les méthodes actuelles de recyclage des composites, comme la pyrolyse (chauffage à haute température pour décomposer les matériaux), peuvent être coûteuses et nécessitent des infrastructures spécialisées.
Solutions et opportunités
- Recherche et innovation : De nouvelles méthodes de recyclage, comme le recyclage par solvolyse (décomposition chimique à l’aide de solvants), sont en cours de développement pour récupérer efficacement les fibres de carbone ou de verre sans altérer leurs propriétés mécaniques.
- Réutilisation des fibres : Les fibres de carbone recyclées peuvent être réutilisées dans des produits de moindre exigence, même si leurs propriétés ne sont pas aussi optimales que celles des fibres neuves.
- Utilisation de composites thermoplastiques : Certains fabricants explorent l’utilisation de composites thermoplastiques, qui peuvent être refondus et réutilisés, ce qui faciliterait grandement leur recyclage à la fin de leur cycle de vie.
- Eco-conception : Dès la conception, il est possible de privilégier des matériaux plus faciles à recycler ou des assemblages modulaires qui permettent le remplacement et le recyclage plus facile des composants.
Initiatives et pratiques
- Économie circulaire : Des initiatives se développent pour intégrer une approche circulaire, en encourageant la récupération des prothèses orthèses et podo-orthèses usagées, leur désassemblage, puis la réutilisation des matériaux récupérés dans la fabrication de nouveaux dispositifs.
- Sensibilisation des professionnels : Former les concepteurs et les techniciens en prothèses orthèses et podo-orthèses à l’éco-conception et aux méthodes de recyclage peut contribuer à réduire l’empreinte écologique de cette industrie.
Avantages environnementaux et économiques
- Réduction des déchets : Recycler les composites pourrait réduire considérablement les déchets générés par l’industrie des prothèses orthèses et podo-orthèses, contribuant ainsi à une meilleure gestion des ressources.
- Diminution de l’empreinte carbone : La fabrication de fibres de carbone ou de verre neuves est énergivore. Le recyclage de ces matériaux permettrait de diminuer l’énergie nécessaire à leur production, réduisant ainsi l’empreinte carbone globale.
- Soutien à une industrie plus verte : La transition vers des matériaux recyclables et des procédés de fabrication plus durables pourrait positionner le secteur des prothèses orthèses et podo-orthèses comme un modèle de durabilité dans l’industrie médicale.
En résumé, bien que le recyclage des matériaux composites des prothèses, orthèses et podo-orthèses soit complexe, il existe des solutions technologiques émergentes et des approches d’éco-conception qui peuvent aider à rendre ce secteur plus respectueux de l’environnement. L’innovation dans ce domaine est cruciale pour répondre aux exigences croissantes en matière de durabilité.
Depuis plusieurs années, de nombreuses voies sont explorées avec plus ou moins de réussite et de pérennité. Souvent les solutions trouvées sont difficilement transposables ou adaptables à notre domaine, ce qui tue en quelque sorte certaines velléités
Dans cette veille technologique, il est intéressant de regarder les initiatives qui sont engagées dans des directions parfois inattendues.
Parmi elles, la start-up Française Bambooneo s’est engagée sur une idée originale. En prenant pour base de travail une matière naturelle : le bambou, l’entreprise propose un travail dans 2 directions : aval et amont.
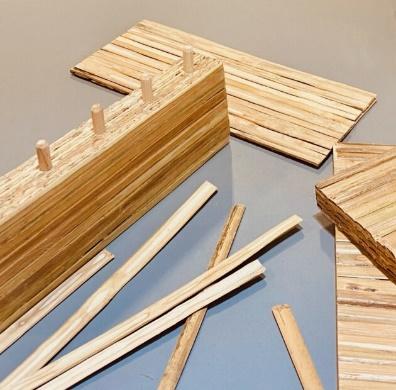
Crédit Photo : Bamboneo
Du bambou pour recycler les déchets composites en les intégrant dans des murs conçus à partir de lanières de bambou, d’une part.
Et d’autre part, des granulés de bambou comme renforts intégrés dans les résines lors des fabrications composites permettant d’abaisser l’empreinte carbone de certains produits.
Dans le premier cas, c’est une « prison » de bambous pour les déchets composites. Ainsi pourrait-on présenter l’innovation de cette start-up. Sa solution, destinée d’abord au secteur du BTP, repose sur un procédé breveté qui permet de produire industriellement des panneaux à partir de petits bambous de 20 mm de diamètre, cultivés en Europe.
« L’entreprise travaille sur des blocs de construction constitués d’une sorte d’exosquelette ou de carapace en lanières de bambou, qui pourra, par exemple, emprisonner des granulats issus de pales d’éoliennes broyées à recycler », précise Bernard Derrien, fondateur de la start-up, créée en juin 2024, qui emploie une dizaine de personnes, menuisiers ou recycleurs.
Une trame en bambou
La première étape du processus, brevetée, consiste en l’éclatement puis au collage entièrement automatisé de 32 bambous par seconde. Ils sont ensuite transformés en panneaux de 80x120cm constitués de 2 couches croisées superposées et fixées grâce à une colle polyuréthane biosourcée à 80 %.
Collés ensemble, ces panneaux peuvent remplacer de l’OSB (Oriented Strand Board, panneaux traditionnellement fabriqués à partir de particules de bois) pour des coffrages, des façades, ou encore des poutres.
Les atouts des composites
L’entreprise les utilise ensuite pour fabriquer des briques de 40×20 cm, de 40 mm d’épaisseur, constituées de 25 lanières de bambou croisées et emboîtables comme des legos. Avec une rigidité supérieure au bois, elles permettent ensuite de fabriquer des murs à double-cloison qui pourront être remplis de terre-sèche mêlée à des écorces ou bien encore, les composites broyés en granulés tels qu’expliqué précédemment.
« On peut remplacer la terre par un broyat de composites sous forme de granulés car l’apport en poids et en inertie thermique est intéressant. L’utilisation de composites comme remplissage permet par ailleurs de recourir à moins d’arbres coupés pour la fabrication des bâtis. Nous essayons dès que c’est possible d’utiliser des déchets à la place de la terre. Cela rend les murs très solides, denses, avec une bonne isolation. Les composites constituent en effet un meilleur isolant que la terre. On peut intégrer 60 kg de composites par m2 de mur », précise Bernard Derrien.
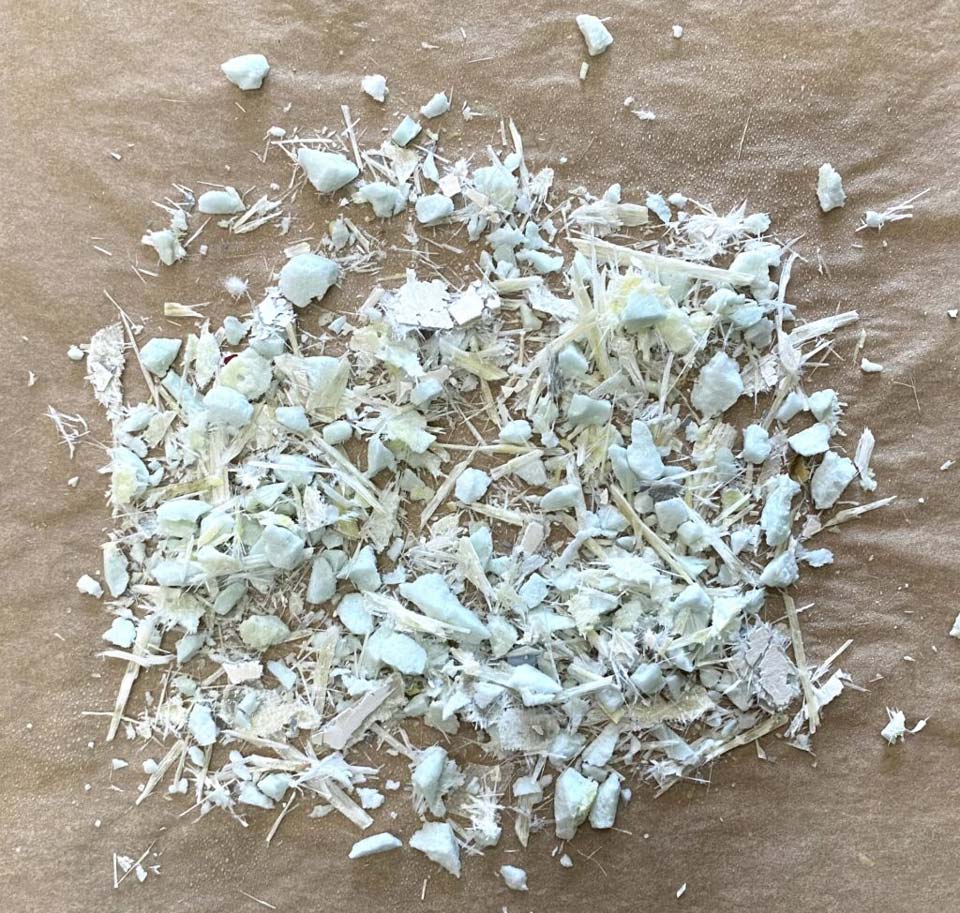
Alléger l’empreinte des composites
Bambooneo se charge de la récupération de la matière première à recycler à la source. « Nous nous occupons de tout, nous nous rendons sur les chantiers avec des broyeuses sur camions pour récupérer des pales d’éoliennes ou des pièces de gouvernails de catamarans comme les safrans. Puis nous les broyons sur place avec trois niveaux de broyage différents selon les besoins. Nous n’avons pas besoin de séparer les composants. Notre technologie s’adapte aussi bien aux rebuts composites de l’automobile que de l’aéronautique ou de la marine », poursuit M. Derrien. Les composites dans les cloisons n’étant pas mélangés avec d’autres ingrédients, ils pourront être réutilisés tels quels en cas de démantèlement des murs.
Pour compléter son offre, l’entreprise propose également un produit destiné cette fois davantage aux fabricants de matériaux composites. Il s’agit de granulats de faces externes de petits bambous de moins de 25mm de diamètre. « Ces renforts compacts et denses comportent plus de lignine que le teck et contiennent également une quantité importante de silice. Certains de nos clients les testent actuellement pour améliorer leur bilan carbone », précise le fondateur de la jeune pousse.
Outre l’aspect séduisant du process, il évoque une voie potentielle pour notre secteur, en particulier l’idée du « broyage sur place » qui constituerait un atout mageur pour nos structures. Car c’est toujours et encore les deux questions qui reviennent sur le dessus de la pile : la collecte des déchets et leur acheminement vers un centre de retraitement.
Gageons que ce sera au travers des avancées réalisées dans les autres secteurs que nous trouverons finallement les solutions adaptées au nôtre.
Alors bien sur, en écrivant ces lignes, c’est bien sur la stimulation de la créativité des plus jeunes que l’on compte pour aboutir dans ce domaine, ainsi qu’aux perceptibles « tempêtes de cerveaux » que ces articles ne manqueront pas d’engendrer chez eux !.. A moins, qu’ils ne nous aient pas attendu !..
Sources : Jec, Bambooneo